What is an encoder?
In industrial automation, an encoder is an electrical device that translates motion data into usable information such as speed, position, count or direction.
In most applications, the information provided by an encoder is sent to a motion control device (such as a PLC, drive or counter) which then sends a signal to another machine to perform a function, for example:
In the automotive industry, on the assembly line, encoders can give positional feedback to robots ensuring welding arms have the right information they need to weld in the correct locations.
In the food industry, servo motors work with encoders and PLCs in precision labelling applications to control the timing and speed of bottle rotation for labelling.
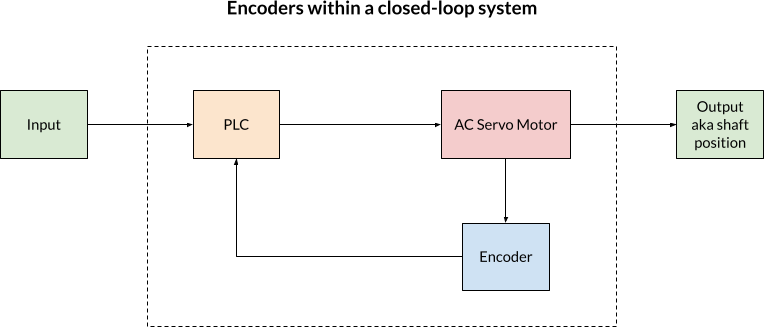
Although there are many different ways to use an encoder and although there are many different ways that an encoder can sense movement (mechanical, magnetic, resistive and optical), there are still only two main types of encoder that people use:
Linear and rotary
A linear encoder uses a transducer to measure the distance between two points whereas a rotary encoder collects data and provides feedback based on the rotation of an object.
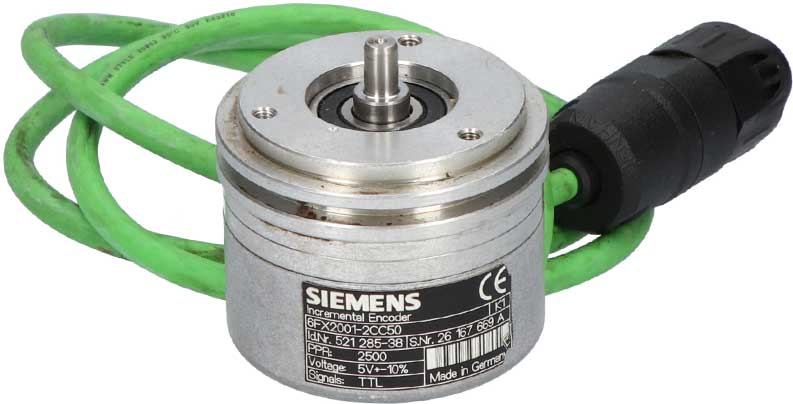
Similarly, there are also only two main types of measurement that an encoder will provide:
Incremental and absolute
Incremental encoders do not provide a specific position; they only tell you the position has changed. In contrast, absolute encoders communicate a specific position by using a unique code pattern to indicate said position.
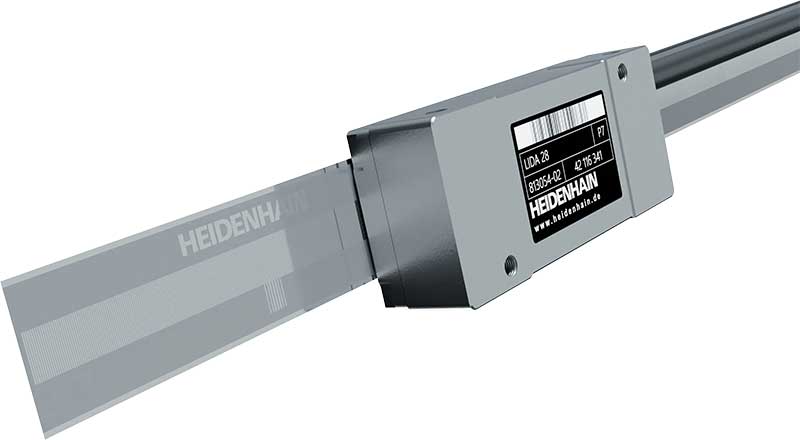
As you can see, speccing an encoder could be a minefield if you don’t know what you are doing. If you want to know more about encoders or how Foxmere can help you with an encoder specification, please call our offices today at +44 (0)1922 349 999 or email us at [email protected].