Cobots to the rescue
According to a late 2024 survey by the National Association of Manufacturers, nearly 60 per cent of employers cited "attracting and retaining a quality workforce" as a primary business challenge. With businesses struggling to find and keep skilled workers, companies are turning to a specific piece of equipment to plug the gap.
Collaborative robots, or cobots, are predominantly designed to work alongside humans in shared workspaces, enhancing efficiency and safety.
Unlike traditional industrial robots that often need to work in isolation to ensure safety for the workforce, cobots are equipped with advanced sensors and adaptive algorithms to interact safely with human operators.
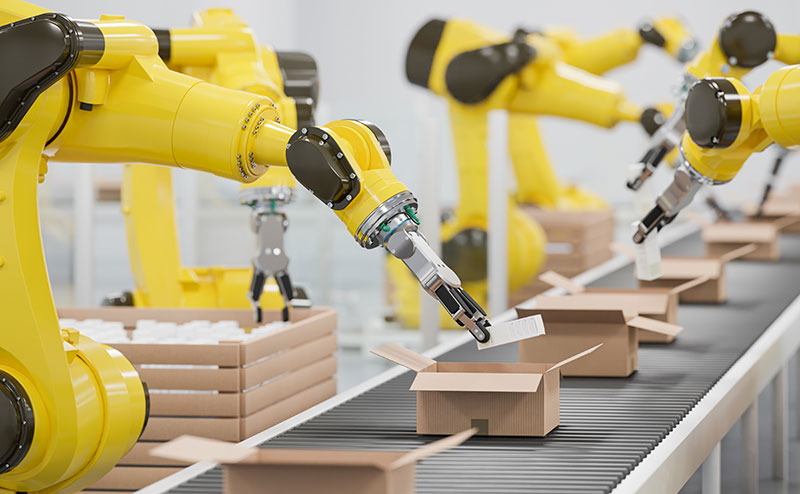
But did you know that, as manufacturers face challenges in hiring and retaining workers, many are turning to cobots to bridge the gap and support their workforce?
Upskilling
Take Emerson, one of the world’s leading engineering and automation companies, as an example. They’ve invested in FANUC cobots to handle tasks like stacking and palletising boxes, taping them together and prepping them for human workers to fill.
This enables companies to enhance worker satisfaction and productivity by freeing employees from repetitive tasks, allowing them to focus on more impactful, skilled responsibilities and usually higher paid jobs.
Jeff Burnstein, president of Ann Arbor's Advancement for Automation Association, reinforced this message by saying, "The types of tasks that robots do, generally, they're dull jobs, dirty or dangerous jobs that people don't want to do, so companies have a hard time finding people to do those kinds of jobs.
"Oftentimes we find the robot is actually allowing the person to do a better job. I can do something that allows me to use my brain more [like] oversee the system, which is oftentimes, a better, safer and higher-paying job, so we don't see robots as replacements for people.”
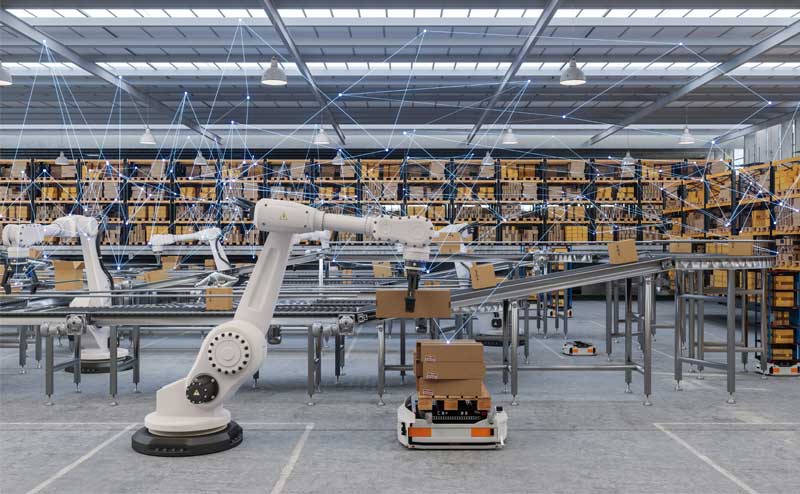
Using cobots also helps reduce injury risks. Having a cobot lift heavy boxes instead of a person means fewer workplace hazards, something that can end up costing companies far more than the robot itself.
For example, a Universal Robots UR30 cobot kit, which can lift up to 30 kg and has a reach of just over 130 cm, is listed for $68,000 on Olympus Controls. For companies like Emerson, that’s a smart investment compared to the potential costs of workplace injuries.
Business case
On the topic of cost, alongside the need to retain staff, cobots play a key role in addressing the broader skills gap. According to a World Economic Forum report, by 2025, more than 50 per cent of employees globally will need to reskill or upskill.
From a financial perspective, upskilling helps avoid the significant costs associated with turnover. When employees leave, companies face expenses like recruiting fees, onboarding costs and the productivity loss from the gap left behind.
In fact, replacing just one employee can cost thousands of pounds when you factor in everything from recruitment to training. In the UK, the average cost to hire someone is around £3,000, or 20-30 per cent of their salary, with more senior roles driving up that cost even further.
The cost of not retaining staff can be even higher. A poor hire, for example, can cost a company 30 per cent of their first-year salary, and 27 per cent of businesses report that bad hires cost them more than £50,000.
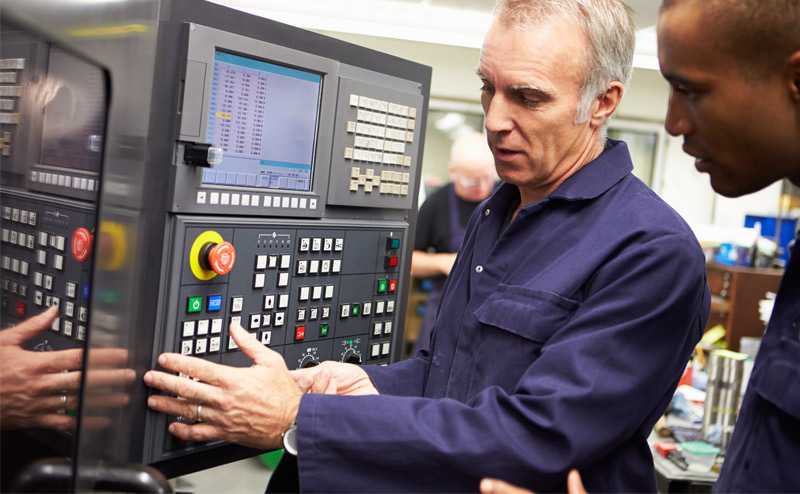
Beyond financial strain, a bad hire can lead to a 36 per cent drop in productivity too, making upskilling a more cost-effective and productive solution.
By investing in the growth of current employees and integrating cobots into the workflow, companies can boost satisfaction and loyalty, making employees less likely to leave and reducing additional financial burdens.
Safer environment
As mentioned, reducing the risk of injury is a key factor in attracting and retaining workers in the manufacturing sector.
In fact, Travelers Insurance’s studies have shown that implementing manufacturing automation, specifically cobots, can significantly decrease the occurrence of workplace injuries. This includes injuries caused by heavy lifting, contact with harmful objects and repetitive stress, with a reduction of up to 72 per cent.
Just look at EVCO Plastics in Wisconsin, deploying cobots to handle the heavy lifting and placing of parts on the packaging line. This has not only created a safe working environment for workers but also led to cost savings through reduced workers' compensation insurance premiums, due to a decrease in repetitive strain injuries.
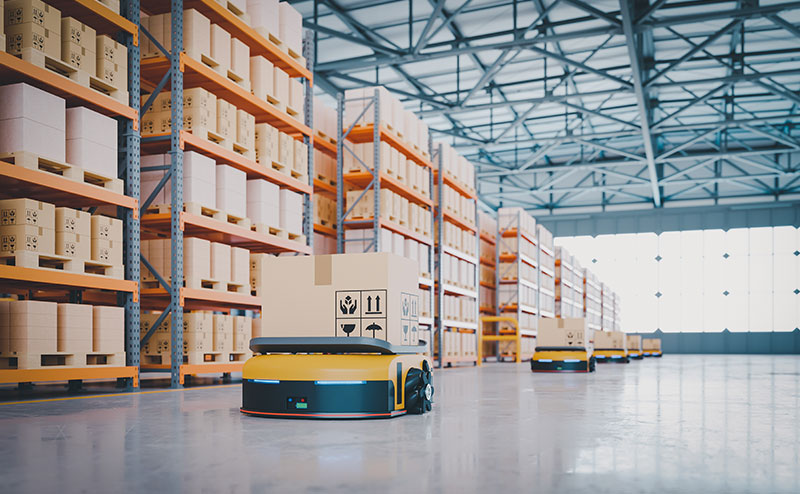
At Foxmere, we see automation as the way to improve efficiency and create a safer work environment. As well as keeping systems running and preventing unplanned downtime, we also help to reduce expenses while supporting efforts to bridge the skills gap.
That’s because cobots aren’t here to replace workers. They’re here to make manufacturing jobs more appealing by enhancing safety, reducing physical strain and providing pathways to skilled roles that keep people in the industry.
Contact us today for a no-obligation quote on automation equipment ranging from replacement or obsolete parts to complete systems.