Smarter maintenance strategies to deal with downtime
Did you know that unplanned downtime is costing manufacturers as much as £40 billion per year? This comes as no surprise given that equipment maintenance can eat away up to 10 per cent of production time, which is 800 hours per year or 15 hours per week for the average manufacturer.
Last year, UK productivity was 24 per cent lower than it would have been had it continued climbing at the rates seen before the global financial crisis. To put this into perspective, the UK’s productivity growth rate was two per cent a year before the crisis and now it’s below one per cent a year.
What does this mean? Well, the UK's productivity has not made significant progress since before the COVID-19 pandemic. Instead, it has been on a relatively weak growth path since the financial crisis.
The UK productivity problem can be summed up in three words — lack of investment. The weak investment is across industries but is especially notable in manufacturing.
Affecting maintenance strategies
Productivity is defined as the efficiency of production of goods or services expressed by some measure. However, the efficiency and effectiveness of productivity are massively influenced by various factors, such as the supply chain.
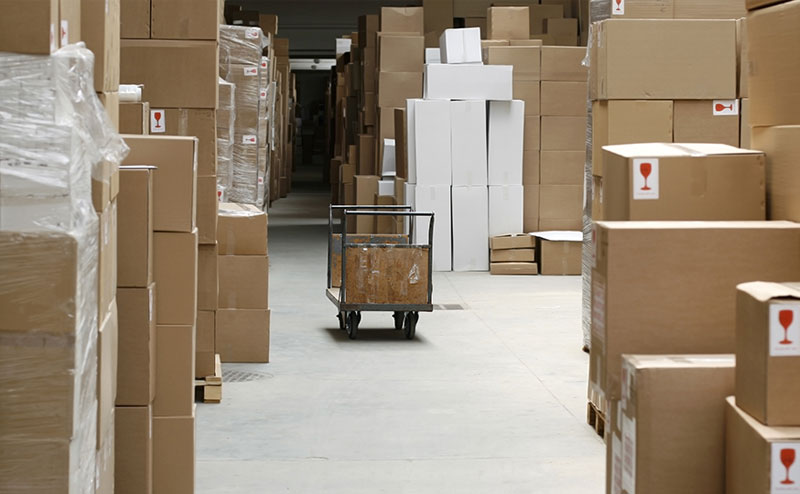
Make UK’s 2022 study revealed that the pandemic disrupted 90 per cent of manufacturers’ supply chains. This can have a huge impact on downtime and therefore productivity, especially when it comes to sourcing replacement parts.
Crucially, this issue becomes even more prevalent when a manufacturer is trying to source an obsolete part.
Overcoming obsolescence
Obsolescence occurs when an original equipment manufacturer (OEM) stops manufacturing a particular product. This could be due to various reasons, such as technological advancements, changes in market demand or the manufacturer discontinuing the product line.
When a part breaks down in a machine or system, food manufacturers may run into the problem of not being able to obtain a replacement directly from the OEM. In these cases, parts can be sourced from reliable suppliers.
This allows food manufacturers to continue operating smoothly without facing extended downtime or the need to fully replace machinery with costly, brand-new equipment.
If food manufacturers then want to improve efficiency, technologies can be retrofitted to legacy equipment.
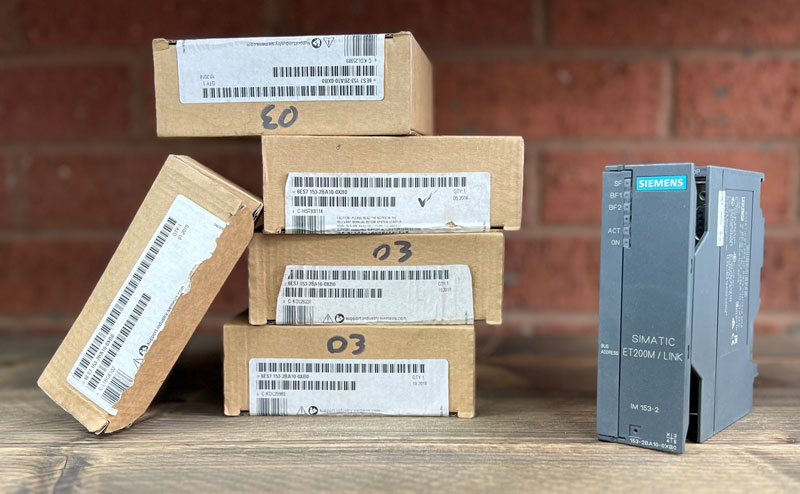
Retrofitting food lines
In a typical food production line, retrofitting may involve upgrading machinery with modern sensors, automation components or control systems to enhance efficiency and functionality without replacing the entire system.
For example, in a biscuit manufacturing plant, retrofitting could enhance existing baking and packaging lines with advanced temperature sensors and automated quality inspection systems.
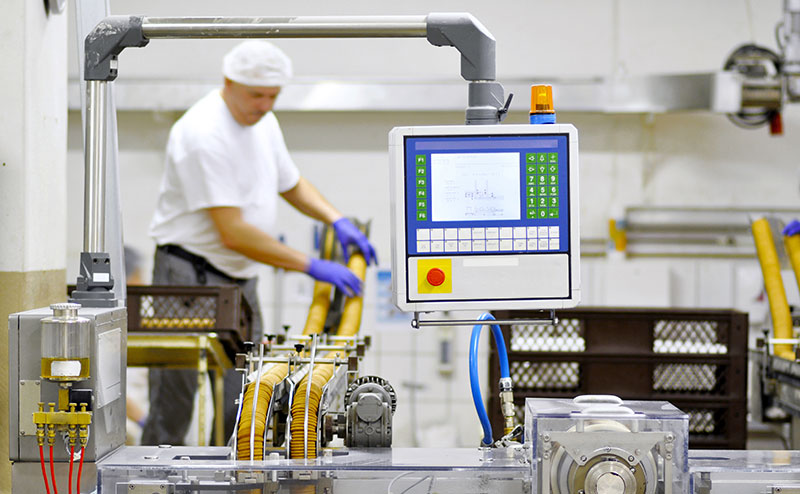
The temperature sensors ensure that the baking process maintains the optimal heat levels for consistent product quality, while the quality inspection systems use cameras to detect broken or misaligned biscuits during packaging.
By implementing these upgrades, the facility can improve product consistency, reduce waste and streamline operations without the need for a complete overhaul of the existing equipment.
A report released by the Good Food Institute and Bright Green Partners claims that retrofitting existing systems allows manufacturers to expand capacity in days or months, compared with up to three years to build a new plant.
On top of that, retrofitting can be done at 20 per cent of the cost.
What’s more, employees and leaders already view automation as a complementary tool, with Harvard Business Review reporting that more than 90 per cent of recently surveyed workers said automation increased their productivity.
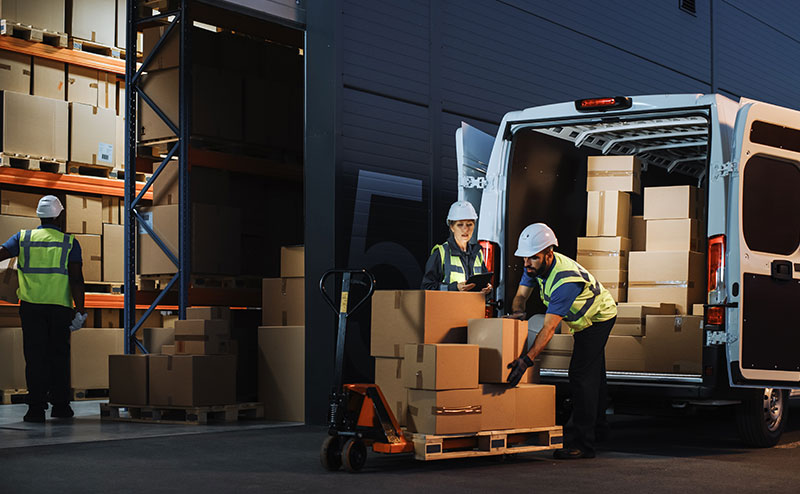
That’s why maintenance strategies should include the contact information of a trustworthy industrial parts supplier and one that can provide obsolete OEM parts, especially with the nature of current supply chains.
And you don’t just have to take my word for it either, with the latest supply chain report revealing that 92 per cent of companies see supplier diversification as a core strategy.
At Foxmere, we understand the turbulence of current supply chains and why having reliable partners is essential for maintaining operational efficiency and improving productivity.
You can contact Foxmere today for a no-obligation quote on a range of automation equipment.
We hold stock of hard-to-find and obsolete automation parts from over 100 manufacturers, and if it’s not in our stockroom, we have access to a curated list of over 500 supply partners from around the world so that we can keep production lines moving, no matter the challenge.