Technology required for Europe’s reshoring efforts
At a time that 58% of UK manufacturing firms are reshoring their supply chains, research from KPMG has revealed that over 50% of firms believe increased digitisation and automation will improve the resilience of their supply chains. Real-time tracking and monitoring systems are also required when strong efforts are being made to bring operations closer to home, providing insights into inventory levels, production progress and shipping statuses. In this post, we explain how manufacturers can increase the resilience of their supply chains when reshoring activities commence.
The impacts of supply chain disruptions have been well documented. In recent times, the COVID-19 pandemic and the war in Ukraine have exposed and exacerbated supply chain vulnerabilities, resulting in shortages, inflation, factory closures and goods waiting at ports to be unloaded, to name a few.
Unsurprisingly, Make UK’s 2022 study revealed that more than 90% of manufacturers said that the pandemic had disrupted supply chains, with a similar number citing Brexit as a cause.
These disruptions can have a detrimental impact on a business. From shipping delays to complete production stoppages, supply chain disruptions leave manufacturers with financial losses, increased costs and reputational damage. But thankfully, there is a growing trend that’s giving manufacturers a glimmer of hope.
Reshoring
Reshoring is the act of relocating your manufacturing and production processes from international (offshore) sites to your local (domestic) sites.
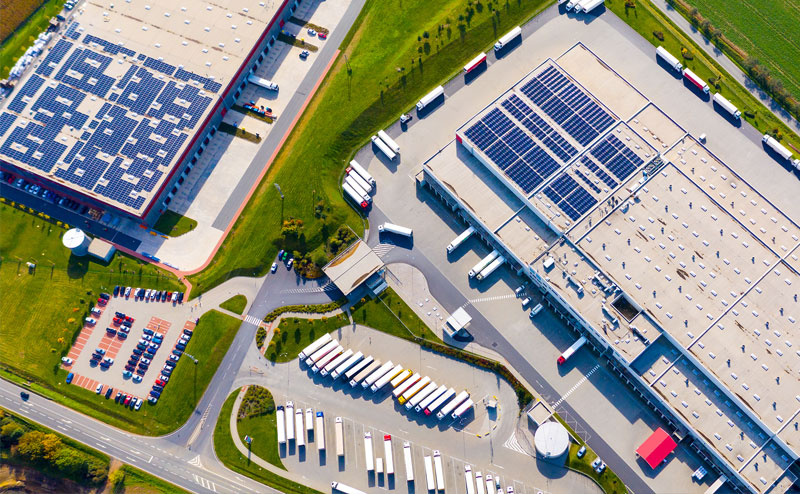
According to research by Medius, 58% of UK manufacturing firms are reshoring their supply chains and 90% of businesses that have engaged in reshoring have had a positive experience.
What’s more, 24% are seeing a reduction in costs, while 26% are reporting enhanced value and heightened security. Not only does reshoring increase transparency for manufacturers, but it also improves quality control and reduces lead times.
These benefits contribute to ensuring that the supply chain is more resilient, so it’s no surprise to see manufacturers reshoring their operations. However, it must be noted that reshoring is not a new business strategy.
Data from Regional Studies, Regional Science states that between 2014-2018 the countries with the highest number of cases of reshoring were the UK, Italy and France. More recently, Belgium has ‘lead’ the charge on the EU’s medicines reshoring plans amid concerns over reliance on non-EU countries.
Initiatives, like Sandoz's new antibiotic plant in Austria, highlight efforts to bolster local manufacturing, addressing shortages worsened by the COVID-19 pandemic and geopolitical tensions.
Tracking systems
Although reshoring is a step in the right direction, tracking systems are needed to provide data to help manufacturers improve supply chain management by highlighting inefficiencies and unnecessary expenses.
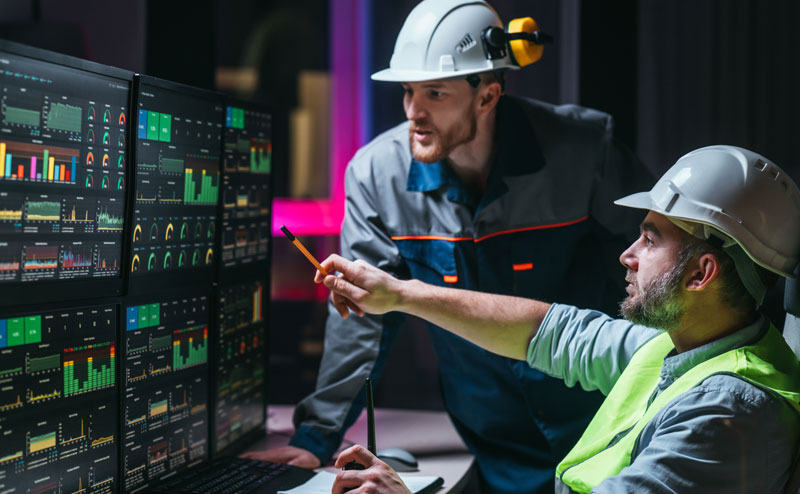
Tracking systems can also alert supply chain managers to any problems during the supply, production or delivery process, helping businesses to act quickly before resources are damaged or wasted. By leveraging software tracking tools, manufacturers can reduce their unplanned downtime, thus realising more profit and improving supply chain resilience.
For example, well-known food manufacturer Kellogg Co uses tracking software to review disparate data sources relating to various demand signals. When it senses a disruption, or a pattern that might lead to a disruption, the software provides a recommendation on how to avoid it. This helps them to adjust and prevent an out-of-stock issue from occurring, days to weeks in advance.
Diversification strategy
Some might say a diversified supply chain is simply a variety of supply and manufacturing channels to meet business needs, but it is much more than that — it is the heart of supply chain resilience.
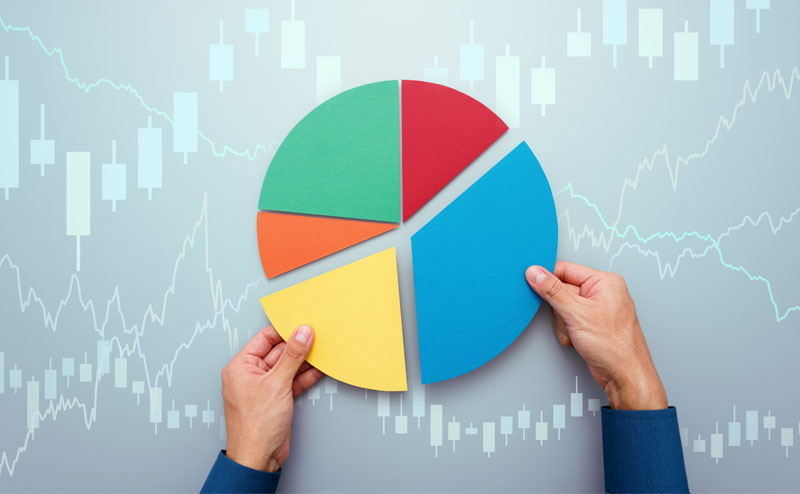
According to the latest supply chain report by reichelt elektronik, 92% of companies see supplier diversification as a core strategy, with 84% switching to local suppliers.
Manufacturers should minimise risk and increase agility by developing a flexible risk management strategy that involves leveraging multiple suppliers, the reimagination of manufacturing and distribution networks and the use of redundant and multimodal logistics methods.
With reshoring and nearshoring gaining traction across Europe, companies need to lean on the support of a reliable supplier to keep the production line up and running. While this may seem daunting for organisations that are comfortable with their existing international suppliers, a data-first approach that continuously monitors supplier information, with a focus on preventing disruption, allow manufacturers to emerge stronger and more resilient in an ever-changing global landscape.
It’s a strategy that we’re passionate about and understand well because, at Foxmere, partnership diversification underpins both our business model and our success. Over the years, we have partnered with over 400 suppliers from around the world, and even if we don’t have a part in stock, we can get it either quickly or affordably, no matter where you are or what industry you work in.
If you would like to know more about how Foxmere can help with your automation spares or if you simply want to discuss digital technologies and require assistance, please contact us via our contact page.