Reviving legacy systems sustainably
According to Intoware's survey, which included more than 1000 UK-based industrial firms, 74% of respondents said they still rely on legacy systems. Although such equipment plays a pivotal role in the operation of many companies, technology is advancing at a rapid pace and is increasing the need for the integration of modern equipment.
Automotive company, Jaguar Land Rover (JLR), is gathering attention for planning new battery plants. JLR's owner, Tata, has recently confirmed it will build a £4 billion electric vehicle (EV) battery factory in the UK.
The recently announced gigafactory will be one of the largest ever investments in the UK automotive sector, helping to grow the economy into clean industries of the future.
However, building new facilities alone is not enough to solve climate issues, as many old machines and structures are still in use today.
Retrofitting
Decommissioning old factories and equipment is expensive and disruptive, plus it can waste resources and energy, thereby contributing to inflation.
Instead, companies can make existing equipment and processes more environmentally friendly through retrofitting — the process of updating or adding equipment or sensors to existing hardware for the use of new technologies.
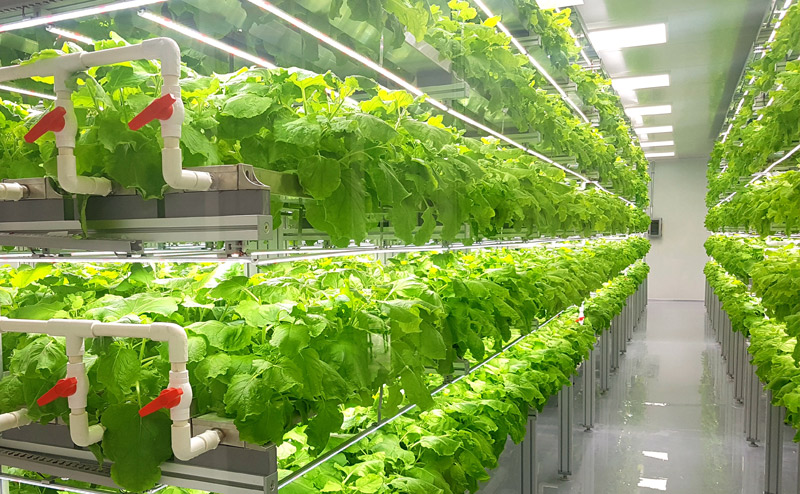
Just look at AGCO, a US-listed manufacturer of farming equipment, that retrofitted its tractors with kit that uses sensors, cameras and artificial intelligence (AI). These kits have helped farmers upgrade their equipment at a lower cost than buying new equipment, reducing costs, waste and even their carbon footprint.
For example, AGCO's sprayer module identifies plants in the field and automatically adjusts the type and the amount of herbicide applied, cutting chemical usage by 70%. Moreover, AGCO's grain storage bin kit detects when a crop is overheating and turns on blowers to move the air around to prevent spoilage.
Scaling up
Retrofitting is a much more cost-effective option than buying brand-new equipment, meaning manufacturers can now scale up to Industry 4.0 quicker and cheaper than ever before.
For example, Felipe Orellana and Romina Torres, two research engineers at the Universidad Andres Bello in Chile, conducted a study on retrofitting legacy equipment with industrial IoT devices in 2019 to create a more efficient smart factory.
The study found that after retrofitting legacy equipment in a spare parts manufacturing factory energy consumption was reduced by 17%, projected costs decreased by 3% and human error was cut by a staggering 70%.
Where to start?
As Intoware's survey revealed, there are still a lot of industrial firms using legacy systems today, but the good news is that 82% believe that data is an asset.
With that in mind, some may require a helping hand when deciding which part of the factory should be upgraded first.
One step we recommend taking is to improve human-to-machine interaction by retrofitting a human-machine interface (HMI) with an easier-to-use graphical interface, such as a touch screen.
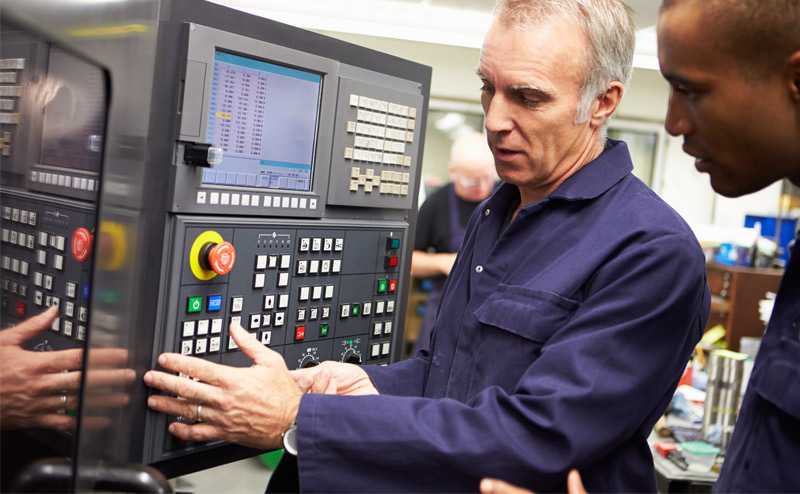
For example, a HMI could be easily integrated into a system by connecting a USB, RS-232 and RS-485 between the HMI and PLC. If the units have wireless capabilities, it can be even easier.
Likewise, smart sensors, which can measure vibrations, temperature and pressure, can also be fitted onto legacy machinery. This allows data to be collected and made available across the whole factory network, which can feed into a predictive maintenance strategy to gain insights into machine performance and upcoming maintenance needs.
If a smart sensor detects that a piece of equipment may break down, the manufacturer can take additional steps to order a replacement from a reliable industrial parts supplier like Foxmere. If you would like assistance in your retrofitting journey or would like to source reliable parts, then please get in touch.