Achieving higher recycled fibre usage
The UK paper industry heavily relies on recovered fibre, which constitues approximately 67 per cent of its raw materials. One of the critical challenges limiting the use of recovered fibre is the loss of paper to the recycling system and the degradation of fibres, which can only be recycled a finite number of times.
Most recovered fibre used by the paper industry is sourced from domestic recycling programs. However, according to Paper Advance, Britain is the largest exporter of collected recycled fibre in the world, with 57 per cent of the collected paper exported rather than used in UK-based production.
It’s also been estimated that the proportion of paper made from recycled fibres is less than 50 per cent of the total fibre used in Europe's paper mills today. That’s despite the fact that, in 2022, 52.6 million tonnes of paper were collected and recycled.
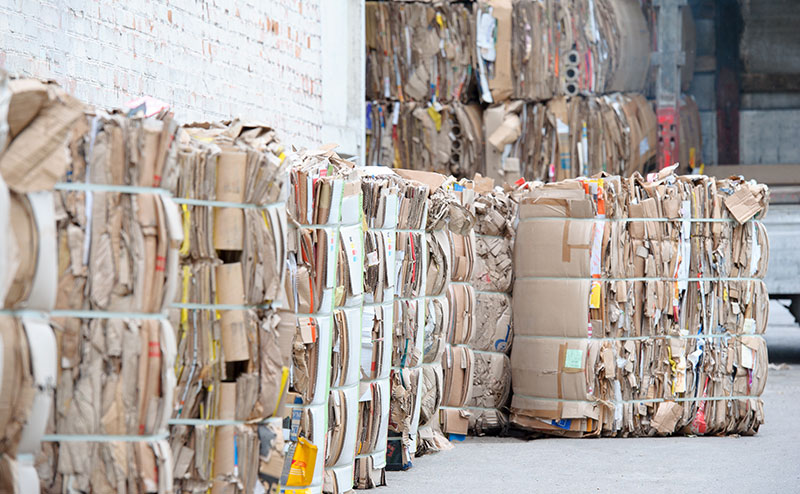
However, not all of the industry’s collected waste products for recycling are used as feedstock in production, which is the raw material to supply or fuel a machine or industrial process, like a paper mill.
Simply put, while a significant amount of paper is being recycled, most of the paper produced in Europe is still made from new or "virgin" fibres rather than recycled ones.
From a raw material point of view, there is room for more domestic production based on recycled fibre, so let’s look at the challenges surrounding the use of recovered fibre in UK-based paper production.
Recycling limitations
Recycling limitations are a significant challenge for the UK-based paper production industry.
Fibres in paper degrade with each recycling cycle, resulting in shorter and weaker fibres that eventually become unsuitable for further recycling. This limitation restricts the number of times fibres can be recycled, imposing a finite lifespan on recycled materials.
Furthermore, as a significant proportion of collected paper is exported, the availability of recovered fibre for domestic use is reduced, limiting the amount of recycled material that can be used by UK paper mills.
Yet these are not the only critical challenges faced by the UK paper production industry, because the loss of paper to the recycling system can occur due to a variety of factors.
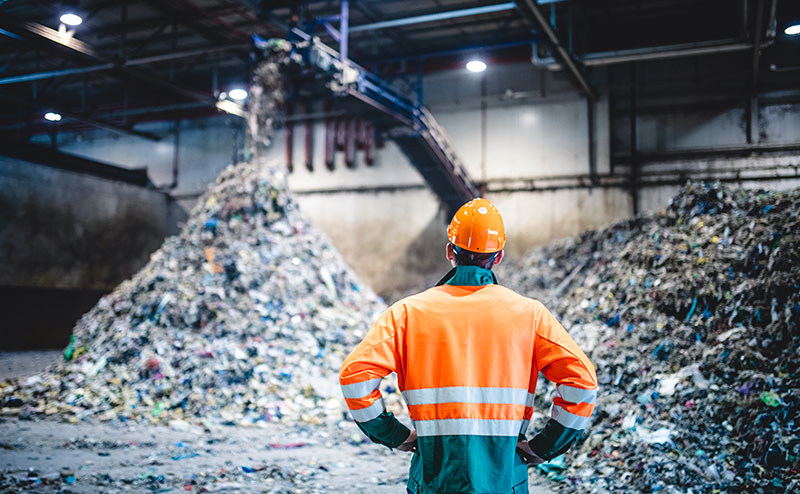
If the collected paper is contaminated with non-paper materials, it will be rendered unsuitable for recycling. Contamination reduces the quality of the recovered fibre and limits its suitability for reintroduction into the paper production process.
Plus, certain types of paper, such as hygiene papers, cannot be recycled and are lost to the system. Hygiene papers, including tissues and paper towels, are often discarded with other waste and cannot be effectively recycled due to their composition or contamination.
This has led to an ongoing need for virgin feedstock in paper production to maintain the necessary quality and supply of raw materials.
The manufacturing process
ISO 14021 defines recycled materials as those that are reprocessed from reclaimed materials by means of a manufacturing process and then made into a final product or component for incorporation into a product.
This definition reiterates the importance of reclaiming materials and ensuring they undergo a manufacturing process to transform them into usable final products or components.
There are both inputs and outputs during any manufacturing process, including those in the paper and pulp industry, but most processes are not fully efficient.
This means that some of the material input is not used to produce the intended output and is instead lost as inefficiencies or converted into waste materials that are not valuable to the papermaking process.
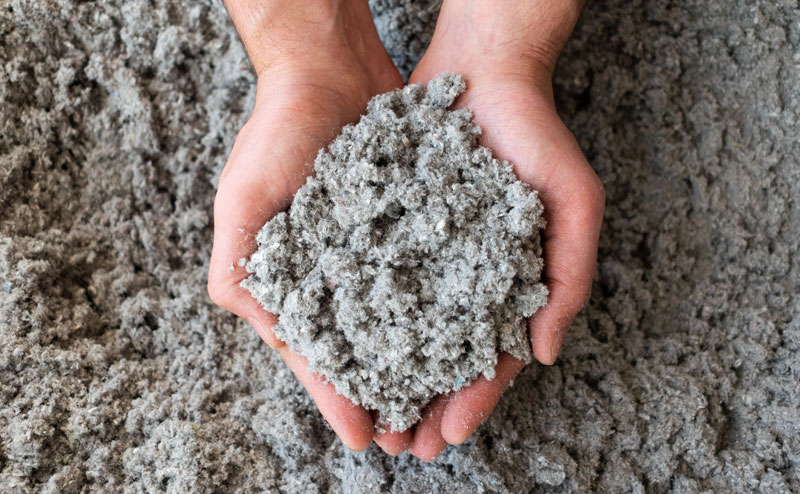
In this context, yield — the ratio of usable paper or pulp produced from raw materials — is a critical metric.
Increasing yield means reducing the amount of raw material wasted and maximising the conversion of input materials into high quality end products. This allows the industry to ensure that more of the collected and processed recycled fibre is effectively used.
Advanced systems
By effectively separating high quality fibres from lower quality materials, advanced sorting systems ensure that only the most suitable fibres are used in the papermaking process.
Quality control systems further contribute by monitoring and maintaining the standards of the fibres throughout the recycling and manufacturing stages.
These systems can detect contaminants and other issues that might compromise the quality of the final product. By identifying and removing impurities early in the process, quality control systems help preserve the integrity of the fibres, thereby extending their usability.
For example, DS Smith's Kemsley Mill implements sorting technologies that allow for the separation of high quality fibres from contaminants and lower quality materials.
This mill, which is the second biggest recovered fibre-based paper operation in Europe, processes around 820,000 tonnes of paper per year, with a substantial portion being recycled fibre.
As a result, the paper mill can turn waste into quality usable materials once again.
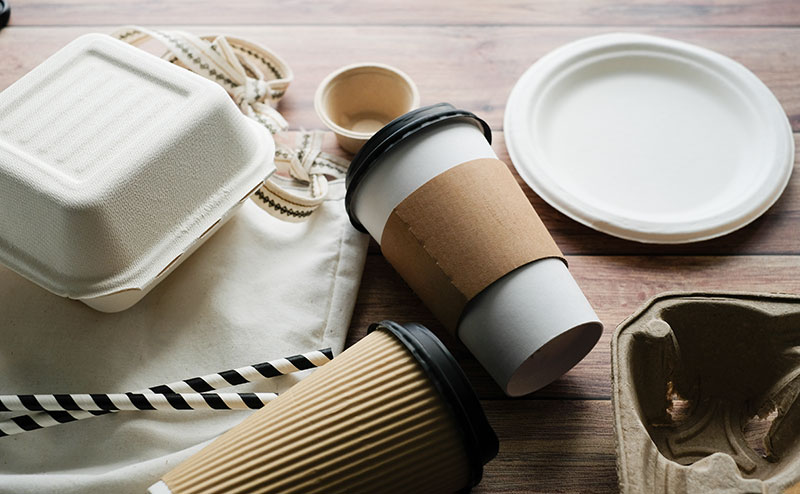
It’s these advanced, automated systems that optimise manufacturing processes to achieve a higher fibre usage and cut down on waste.
Through automation parts suppliers, like Foxmere, paper mills are provided with the necessary technologies that the UK’s paper and pulp industry needs.
With room for more domestic production based on recycled fibre, sorting and quality control systems are a must for improving the quality of recovered fibre and increasing the yield of usable material.
If you would like assistance finding the right automation part for your pulp and paper production process, please get in touch via our contact page.