The controller conundrum: PLC, PAC or IPC?
At the heart of any automated setup is the controller, a decision-making hub that monitors and controls industrial equipment and its motion. However, the choice between a PLC, a PAC or an IPC hinges on a series of crucial decisions dictated by the specific application — a challenge that many plant managers still face today.
The distinctions between programmable logic controllers (PLCs), process automation controllers (PACs) and industrial PCs (IPCs) are often nuanced rather than clear-cut.
Adding to the confusion, manufacturers frequently label their products using the terminology preferred by their target market instead of strictly adhering to traditional definitions.
So, here's a simplified perspective.
A PLC is considered the foundational, standard controller that is primarily designed for straightforward, robust control tasks. A PAC, on the other hand, builds on the capabilities of a PLC, offering additional features and greater flexibility for more complex automation needs. Meanwhile, an IPC can run the same software as a PAC but includes all the capabilities of a personal computer, providing extensive processing power and connectivity options — but what are the differences between each of these controllers?
PLCs
Engineer, Richard E. "Dick" Morley is widely acknowledged as the pioneer of the PLC. In 1968, he created the first semiconductor-based PLC, named the Modicon 084, to replace the cumbersome and inflexible hardwired relay systems of the time.
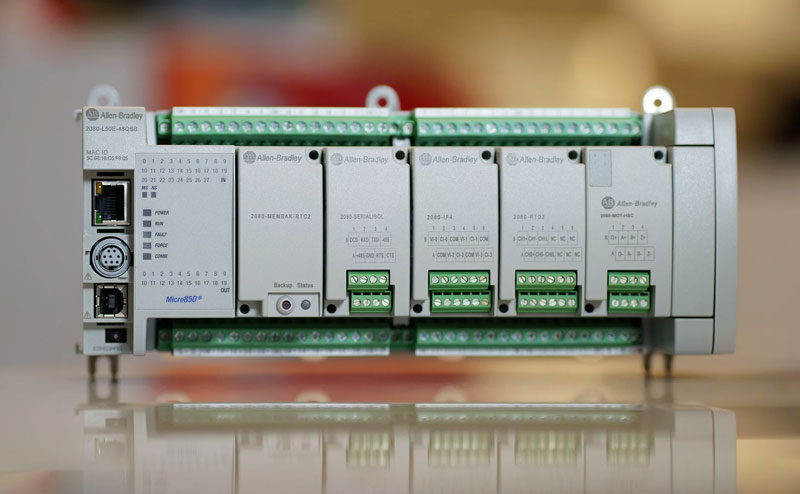
Today’s PLCs execute preprogrammed instructions, often in ladder logic or other structured languages. Usually used in conjunction with SCADA systems, they monitor inputs from sensors, make logical decisions and control outputs to actuators, like motors.
In addition, their cost-effectiveness makes them a popular choice for small-scale projects. Advanced PLC models can handle remote Input/Output (I/O) and motion control, providing greater flexibility and functionality for complex automation tasks.
For example, in the food industry, A PLC could be used to detect burnt potato chips on an assembly line and automatically remove them, ensuring product quality and efficiency.
PACs
Unlike PLCs, PACs use exception-based logic rather than ladder logic. The system can, therefore, handle events or exceptions as they occur rather than following a sequential process.
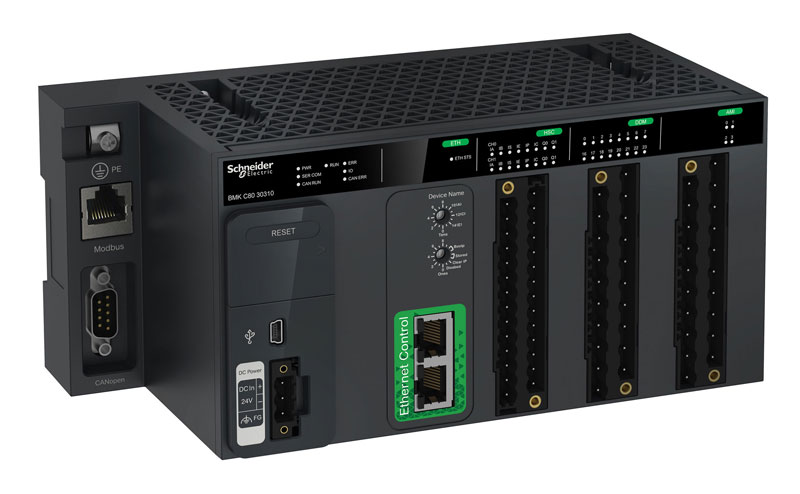
This means that PACs can efficiently manage complex applications, such as advanced process control and motion control, by responding dynamically to real-time changes and conditions in the system.
For instance, a PAC could control high-speed multi-axis robots, manage sophisticated vision systems or conduct extensive data logging, all while seamlessly interfacing with SCADA systems and Human Machine Interfaces (HMIs).
However, while PACs generally offer more advanced functionality and better performance, they are also more expensive than PLCs. However, as technology advances and R&D costs decrease, the distinction between the two types of controllers is likely to become less clear.
IPCs
An industrial PC is a rugged computer designed for industrial or harsh environments.
Like a PC, an IPC can support standard hardware interfaces, such as USB and PCI, ensuring easy integration with various everyday peripherals. Engineers can also use frameworks like .NET and tools like Visual Studio to create customised applications and interfaces for specific industrial needs.
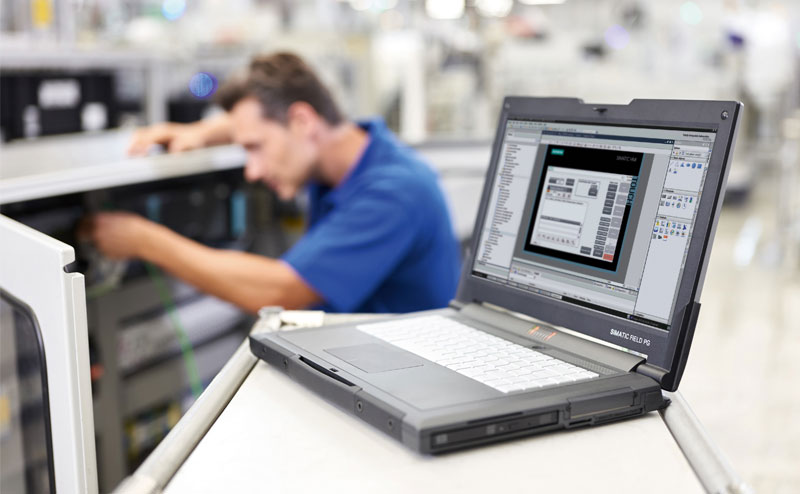
IPCs can also manage tasks parallel to the operating system (OS). This means that critical real-time tasks, such as control processes or data acquisition, can operate independently and concurrently with the OS without being disrupted by changes or updates to the OS itself.
IPCs can offer so much flexibility, and that’s before mentioning that their operating systems allow the use of media players, PDF viewers, text editors and CAD suites, which generally makes life easier.
It’s this versatility which has made IPCs a popular choice with engineers since the 1990s.
Which one to choose?
PLCs are often ideal for standalone machines. Yet if motion control, safety integration or managing remote I/O are needed, a PAC is typically the better choice. For applications with advanced features or extensive software requirements (beyond what a PAC could provide), an IPC could be the appropriate solution.
However, if the total cost of ownership is a determining factor, investing more initially can save money over time by meeting future scalability needs and enabling data-driven process improvements.
Strategic upfront investments can, alternatively, yield substantial long-term savings and operational efficiencies, ensuring that businesses meet immediate growth needs and optimise processes through valuable data insight.
Whatever your controller conundrum, automation parts suppliers like Foxmere, can supply and advise plant managers on the right, cost effective controller for their application. If you would like assistance sourcing a PLC, PAC or IPC, please get in touch via our contact page.