Futureproofing: Mitigating the cost of poor quality
We might think that futureproofing in business has to involve something futuristic and cutting-edge, and sometimes it does. But more often than not, being prepared for the future comes down to looking after what we already have.
Quality control and quality assurance are core elements of any type of manufacturing. But we don’t often talk about the actual cost of quality, or rather, the Cost of Poor Quality (COPQ).
Popularised by IBM’s H. James Harrington in the 1980s, the COPQ is the sum of all costs to a business that would no longer exist if all systems and processes were perfect. These costs can be either directly or indirectly related to quality. A similar concept, which we have covered before, is the total cost of ownership.
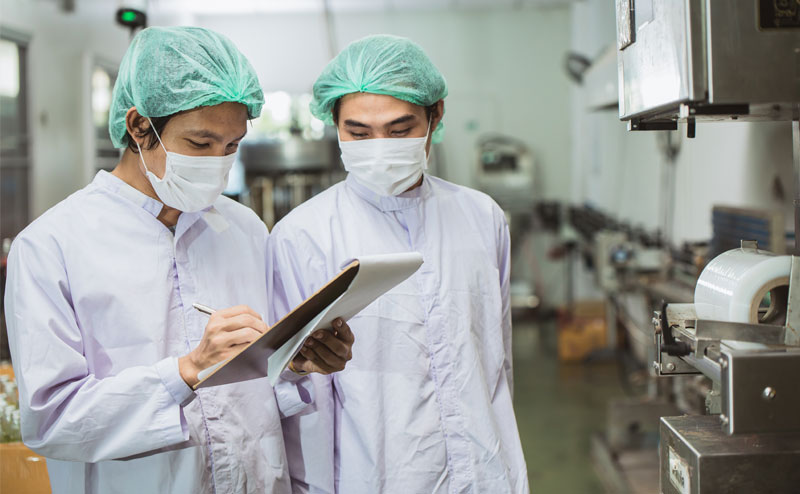
Some direct quality costs are controllable, like inspections, tests, audits, and maintenance. These are the costs of quality. Other direct costs are resultant or unplanned and are incurred by problems with quality (e.g., a machine breaking down). We already know which of these costs is likely to be greater.
Then there are the indirect costs of poor quality:
- Part repairs and/or;
- New parts;
- Human labour;
- Reduced/lost business due to broken machinery and;
- Reputational damage (Ouch!)
Using a wider lens
If we take a step back and consider all of the possible costs of quality in manufacturing, the ripple effect that poor quality can have on profits can be quite staggering.
The average manufacturing firm spends around 20% of its revenue on quality; that’s £2m a year for a company with an annual revenue of £10m, and £86b for the entire UK manufacturing industry as of 2022.
Yes, some of this money will be spent on good quality, but a lot of it will also be spent on poor quality and unplanned downtime, and all of this is time and money that could be better spent on HR, R&D and growth.
Intelligent quality control
We’ve already touched on some of the main contributions of AI to futureproofing in manufacturing, and one of these is machine vision, which allows a computer to "see".

Once implemented, machine vision also represents a significant saving for manufacturers, not only in inspection costs but also in reduced resultant costs of poor quality. In fact, AI-powered defect detection is set to be a game-changer and is already yielding impressive results.
However, for companies not yet ready to implement such a system, there are still fundamental and highly effective steps that can be taken, with a lower barrier to entry:
- Practise preventive maintenance to extend the lifetime of your equipment and reduce unplanned downtime.
- Keep stock of critical spare parts. Don’t wait until something breaks!
- Buy genuine parts, even if they’re used. When you buy refurbished parts from Foxmere, you not only receive them with a full warranty, but you’re also buying sustainably.
If you would like to chat about the cost of quality, or if you are simply looking to buy automation parts contact Foxmere today.