Futureproofing: The future is AI, but what does that mean?
We've all heard that we need to embrace AI to stay ahead of the curve, especially in automation and manufacturing. But what does that look like? In this first instalment of our Futureproofing series, we look at some of the best use cases of AI in automation and some of the most accessible forms of AI implementation.
As we hurtle towards Industry 5.0, businesses are racing to integrate artificial intelligence into systems and decision-making processes in a meaningful way.
This is especially true in manufacturing, where – according to a recent Forbes report – AI is set to be worth more than 20 billion US dollars by 2028. It's perhaps no surprise that 93% of manufacturers reportedly view AI adoption as a top priority for 2024 and beyond, with many prepared to dedicate significant portions of their technology budgets to AI implementation.
AI-powered predictive maintenance
Of all the AI use cases in manufacturing, AI for predictive maintenance is perhaps one of the most effective we've seen. In fact, according to McKinsey, early adopters are already enjoying significant reductions of up to 50% in machine downtime, as well as boosts in productivity (15-30%) and throughput (10-30%).
For example, look at these real-world use cases:
- Mobility conglomerate ZF Friedrichshafen uses AI to gather data from vibration sensors to accurately predict 99% of tool fractures in its gear-part production.
- PepsiCo subsidiary Frito-Lay has used AI-powered predictive maintenance to reduce its planned downtime to 0.75% and unplanned downtime to 2.88%.
- Mondi Gronau used machine learning to implement a predictive maintenance solution that saves them more than 50,000 euros per year in unplanned downtime, allowing them to produce over 18 million tonnes of plastic per year and operate 24/7, 365.
- 3B-Fibreglass uses deep-learning machine vision to predict glass fibre failures up to 75 seconds in advance, reducing a major source of production inefficiency.
Computer vision in manufacturing
As well as predictive maintenance, we are seeing a rise in the number of AI solutions that use computer vision, or "machine vision". This is when a computer processes data points from a visual input to "see" what is in front of it, much like a human. For example, in a quarry, a dump truck might use radar or thermal imaging to help it see through dust.

Furthermore, machine vision can form the basis of an effective predictive maintenance system by predicting when a fracture or breakdown might happen, as in the case of 3B-Fibreglass.
Computer vision can also be used to spot defects, automate quality, pick and pack parcels, count items, classify and sort waste, monitor safety in the workplace, and identify hazards, amongst a host of other industrial applications. Needless to say, these uses heavily depend on in-house AI capabilities, data infrastructure, and specific operational contexts.
Digital twins
Another highly sophisticated use of AI is in the form of digital twins. A digital twin is a virtual model of a physical object, such as a single machine or an entire factory floor.
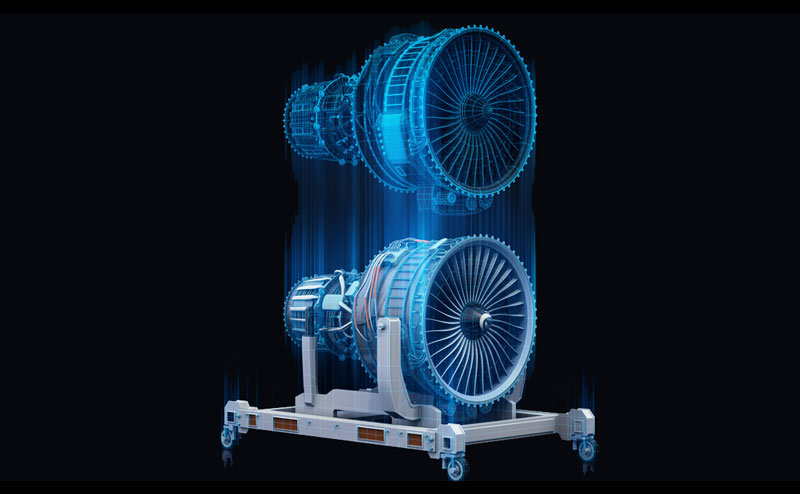
Digital twins can emulate real-world conditions and allow manufacturers to safely experiment with different scenarios across various production processes without interfering with the physical machines. If this is effectively implemented, digital twins can be seamlessly integrated into decision-making processes to run a plant efficiently and with minimum losses.
In a survey, McKinsey found that 86% of senior industrial executives saw digital twins as being highly applicable to their production operations. Still, only half of these had already implemented the technology. In the near future, however, with increased data availability and AI readiness, we can expect to see widespread use of these models and an impressive ROI for those bold enough to explore this cutting-edge technology.
But AI can also look like…
If slick AI integration sounds like a distant pipedream for your business, remember that there are also many accessible ways that AI can be used in day-to-day operations:
- If your website has a chatbot or virtual assistant, you are already utilising AI in a way that supports your team and your customers, freeing up your human resources for more nuanced and complex tasks.
- AI can be an invaluable tool in emails, marketing and communications, whether this is through personalised email marketing campaigns or tailored content based on audience segments. There's no shame in using ChatGPT or Grammarly to get feedback on your written content or generate new ideas.
- Many businesses are already using AI in their data analytics. Using tools like Tableau or PowerBI, you can leverage their built-in AI capabilities to make sense of large amounts of data and extract insights to help inform business decisions.
What is Industry 5.0?
This time last year, we discussed Industry 4.0 and what it meant for automation. Now, we're already looking to the next iteration: Industry 5.0.
Going beyond the implementation of digital technologies such as AI, Industry 5.0 focuses on collaboration between humans and machines, putting humans at the centre.
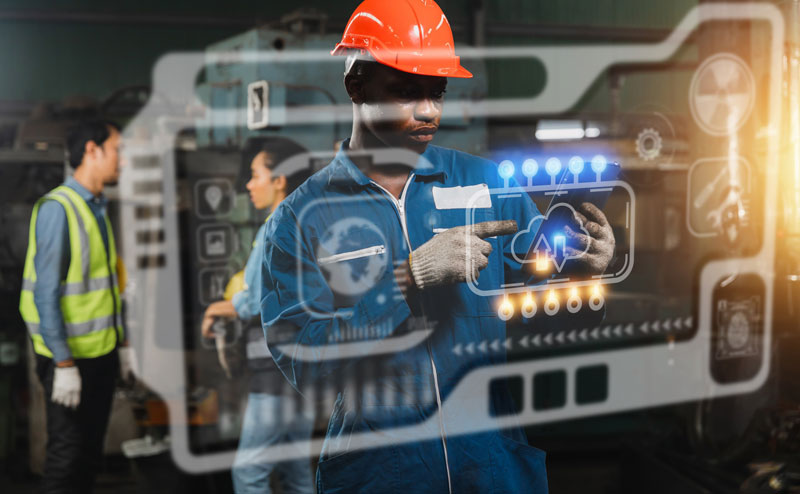
It also has an important focus on sustainability and resilience, with a particular emphasis on social value rather than solely economic gains.
It's something we're really passionate about, and in a recent edition of the Financial Times, our director, Tom Cash, was published for his progressive opinion on the topic of AI in the workplace.
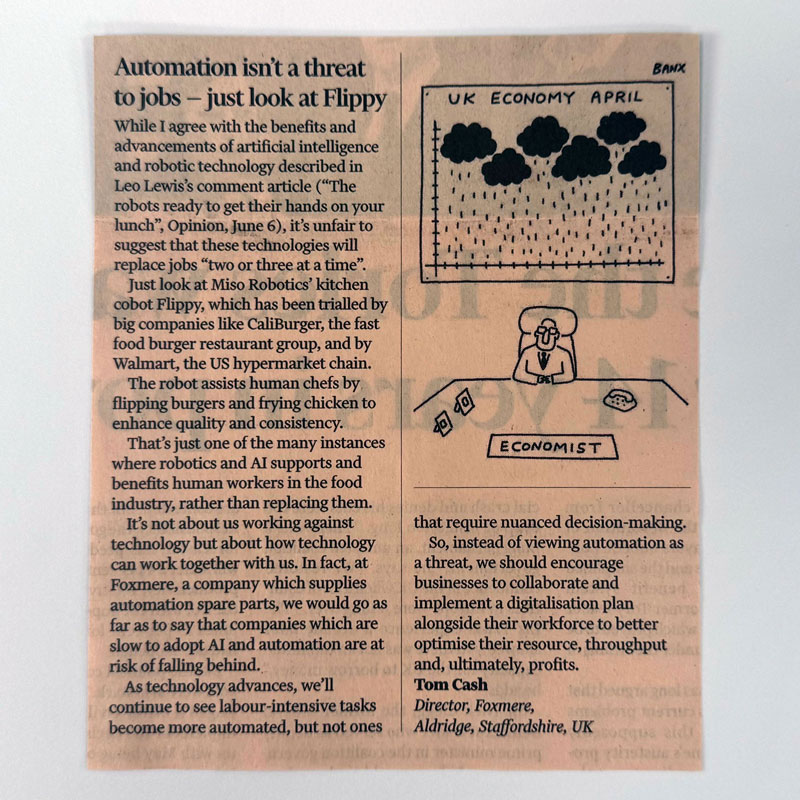
At Foxmere, this is how we view the future of AI:
Instead of viewing automation as a threat, we should encourage businesses to collaborate and implement a digitalisation plan alongside their workforce to better optimise their resource, throughput and, ultimately, profits.
If you're curious about other ways of futureproofing your business, stay tuned for the next instalment in our Futureproofing series, where we'll discuss the importance of quality control. In the meantime, if you would like assistance with your digitalisation plan or if you are simply looking to buy automation parts please get in touch.