What is preventive maintenance?
Preventive maintenance seeks to maximise the operational efficiency, reliability and lifespan of industrial equipment and machinery through planned downtime and maintenance.
Broadly speaking, preventative maintenance involves monitoring the quality, performance and age of industrial components to schedule planned downtime for part repairs and upgrades.
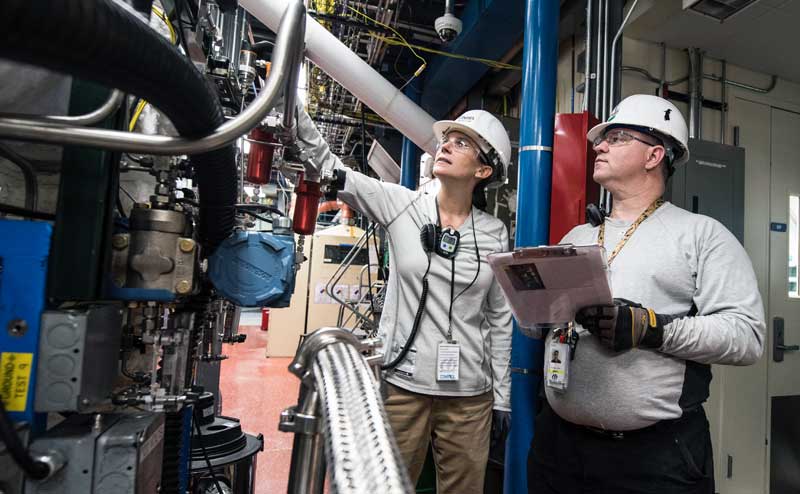
The benefits of preventative maintenance
By implementing preventative maintenance, organisations can achieve higher equipment reliability, reduce unplanned downtime, increase productivity and drive continuous improvement.
The practical costs of unplanned downtime
Those who don’t schedule their downtime can expect to pay more for maintenance and overtime to get work done. Equally, leaving procurement until the last minute can also find you paying more for spares and, ultimately, downtime.
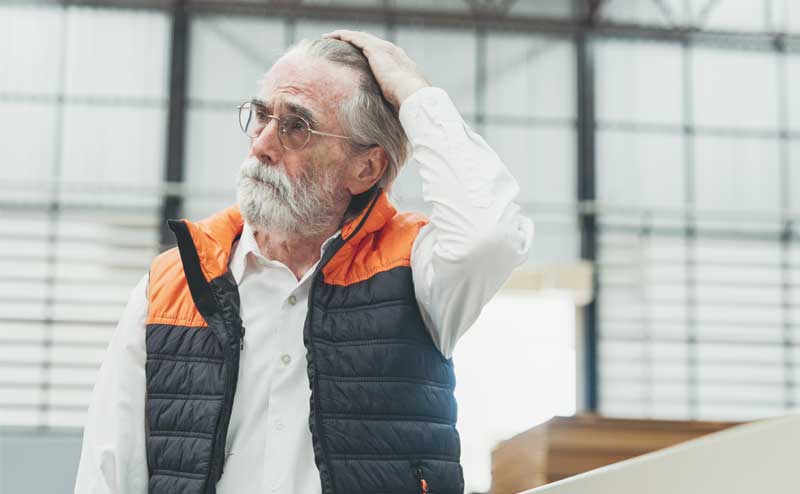
What's more, a lack of planned maintenance typically results in poor equipment reliability and increased order backlogs.
Types of preventative maintenance
There are a few effective preventative maintenance paradigms for manufacturers to follow. Here are the four we experience the most:
- Planned maintenance involves performing equipment maintenance during scheduled downtime when parts and engineers are readily available. Many manufacturers will perform their planned maintenance in line with industry-wide seasonal shutdowns such as Easter, Whitsun, Summer and Christmas.
- Predictive maintenance, sometimes called condition-based maintenance, uses sensors, gauges and other measurement devices to detect early signs of equipment failure. These technologies can identify potential issues before they become critical, allowing maintenance teams to plan for their downtime.
- Time-based maintenance, similar to predictive and planned maintenance, involves performing regular maintenance based on a predetermined schedule, such as daily, weekly, monthly, quarterly or even annually. These schedules are usually defined by the OEM specifications or based on industry best practices.
- Total Productive Maintenance (TPM) focuses on maximising the lifetime value of components by involving more employees in the maintenance process. This approach emphasises teamwork, continuous improvement and a proactive approach to maintenance. Developed in Japan in the mid-1900s, TPM is the most comprehensive and standardised approach to preventative maintenance.
Conclusion
Daily, we’re alarmed by the number of plants and factories that don’t implement some form of preventative maintenance schedule.
Somewhat understandably, those with limited resources believe that preventative maintenance is "nice to have", expensive and complicated.
This couldn’t be further from the truth.
Those that don’t plan their downtime pay more for it practically and financially, and there’s no need.
We have listed four of the most common preventative maintenance methods we encounter here at Foxmere. However, there are so many variations on preventative maintenance that there’s a pattern to fit every application.
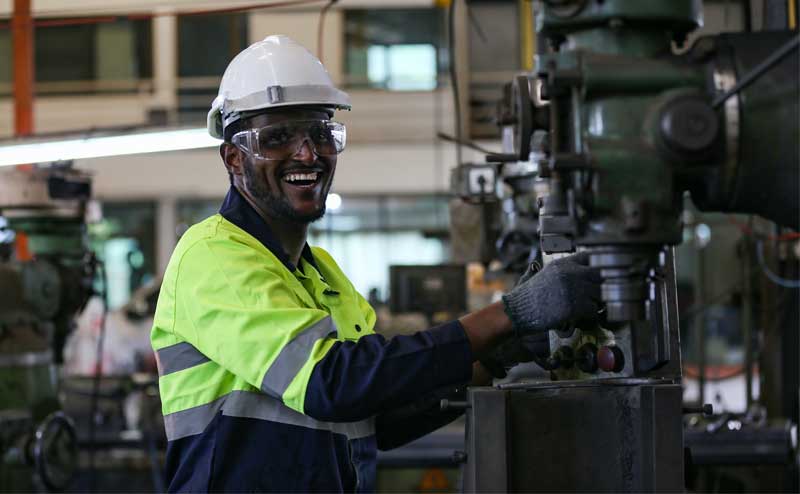
To keep your business moving, implement a preventative maintenance schedule and call Foxmere with your list of critical spares.