Working with obsolescence
Obsolescence occurs when parts are no longer maintained or supplied by their OEM even if said parts are still in perfect working order.
All year round, new regulations, advances in technology and market changes will force OEMs to renew their skills, hardware and software thus making older equipment and services obsolete but, for the end user, there is often no obligation to upgrade.
For many, the cost of upgrading is often seen as not economically viable for a number of reasons:
- The cost of downtime outweighs the cost-benefit of the part upgrade
- The new part is simply too expensive and the existing part works just fine
- There are too many touch points that will need upgrading if this single part is changed and/or the system may need a redesign
- Software is behind by a lot of major versions
- New training may be required
As a result, many of today's production demands are met by plants and factories that are strategically running obsolete hardware and software.
Some may know this as reducing the "total cost of ownership" (TCO) and we think that this is a great concept that can be applied to multiple areas of any business.
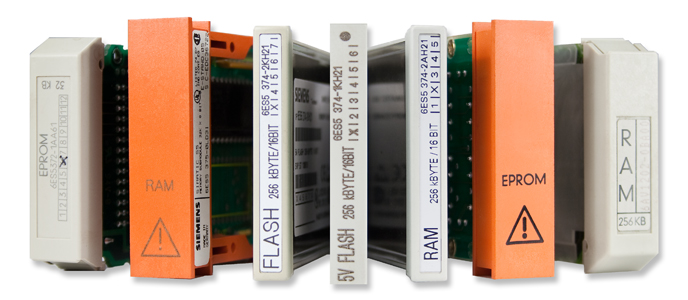
However, there often comes a point where holding on to legacy equipment becomes more costly than one might realise and this is what engineers need to be aware of so that they do not accumulate too much technical debt.
Technical debt is primarily a concept used within software engineering but the broad idea applies here too:
Technical debt occurs when engineers take shortcuts to implement faster or cheaper solutions upfront that are harder to maintain or less efficient to work with long-term.
So, whilst it might be easier to replace parts on a like-for-like basis it must be considered that maturing hardware inevitably becomes more susceptible to failure and, due to declining availability, harder to source and more expensive to purchase.
At this juncture, you may be asking yourself: So, what is it? Do I replace parts and avoid technical debt? Do I strategically make the most out of my existing system and reduce my total cost of ownership?
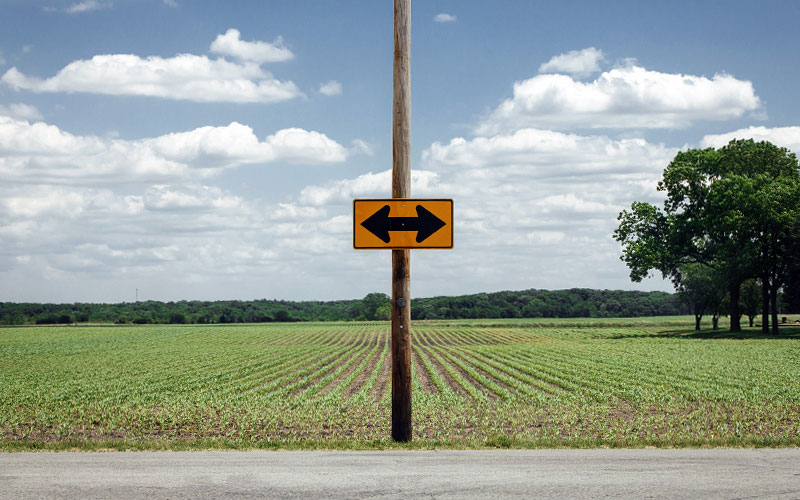
The answer is simple: You do what is best to minimise downtime.
The costs of unplanned downtime can be devastating as system-wide outages often result in not being able to deliver services to customers and losing production time on a critical asset and, in 2018, a study from Aberdeen Research estimated that the cost of unplanned downtime, across all businesses, was a staggering £187,000 ($260,000) per hour.
So, where do you begin?
One of the sure-fire ways to minimise your exposure to unplanned downtime is with careful and regular management of your existing parts.
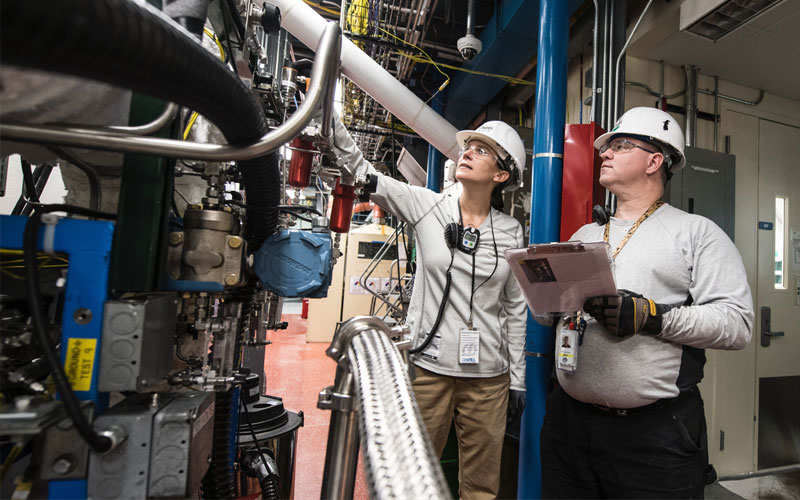
It doesn't have to be complicated either — if you don't have access to, or the budget for, specialist software then a simple spreadsheet should do the trick.
On your spreadsheet you will want to keep a line for each part and you want to ask yourself a series of questions about it, for example:
- Is it system critical?
- Is the software up to date?
- Is the hardware and software still supported by the OEM?
- When is this part scheduled to become end-of-life?
From this list you will be able to quickly spot your exposure to risk and plan for it, asking yourself a series of questions about each part that is due for obsolescence or that is obsolete already.
For example, if a part is obsolete you might want to ask yourself the following questions:
- What is the average lifespan of this part?
- How long do we think this particular part will last?
- Considering downtime, what will be cheaper: Preventative maintenance to upgrade this part now or addressing the issue when the part eventually breaks?
- Is there a replacement from the OEM?
- What is the part number? *
- Where can I get it?
- What is the cost and what is the lead time?
- If I replace this part, will I need other parts too, such as new cables, connectors or connecting parts?
- Are there spares available?
- Where can I get one?
- What is the cost and what is the lead time?
- Should we consider stocking spares of this part?
- When is my last time to buy?
* Some manufacturers have reference tools which can help you when trying to identify successor parts, for example:
- Siemens' Industry Mall
- Schneider's Product Substitution Tool
- Allen-Bradley's Product Lifecycle Search
- Omron's Product Lifecycle Status
- SICK's Phased-Out Conversion List
Once you've completed your list, speak to a company like Foxmere, or your existing parts supplier, and find out their options. For example, buying alternatives to "new" parts is an effective way to keep costs down when stocking critical spares.
- Do they have only the latest parts from your OEM or do they stock both current and obsolete components?
- Is there a range of options to choose from, such as new, refurbished and used?
- Can you get your part repaired?
- Do used and refurbished items come tested and/or with a warranty?
- What are the leads times and costs associated with your preferred options?
Once you have all this information you can finally begin to formulate your plan, purchasing critical spares, new parts and scheduling maintenance with the goal of avoiding unwanted periods of downtime.

Finally, keep on top of your list.
Obsolescence isn't a one and done type of affair — obsolescence is happening all year round. Make the time to check your list on a regular basis so that it doesn't become stale or a chore to maintain.
Good luck!
If you want to know more about managing obsolete parts and ageing systems or if you simply need current or obsolete components you can call us on +44 (0)1922 349 999 where our expert team will be happy to assist.