Mastering motor control
In industrial facilities, electric motors drive everything from conveyor belts to fans and compressors. Now, with the cost of energy rising, manufacturers are trying to find new ways to reduce consumption — and motors are in the spotlight.
Though essential, electric motors are power-hungry, consuming around 50 per cent of the world’s electricity, according to the European Union. Growing energy costs and the need to reduce carbon emissions are both pressing challenges for production facilities, and electric motors have the potential to make a huge difference to both.
A UK Government survey found that over six in ten (66 per cent) manufacturers have taken steps in the past five years to improve energy efficiency, including everything from cultural changes to building improvements.
Another option is to limit the speed and torque of industrial motors so they meet the application’s demand while consuming minimal energy. This can be achieved using industrial drives, including AC drives, DC drives, servo drives, stepper drives and soft starters.
Soft starters
If an application uses an AC motor, manufacturers can retrofit a soft starter to control the output of the motor’s powertrain during its start-up phase.
This smooth acceleration reduces the sudden mechanical shock that occurs during direct-on-line (DOL) starts, which can otherwise cause wear and tear on the motor and connected mechanical components, like shafts, gears and belts.
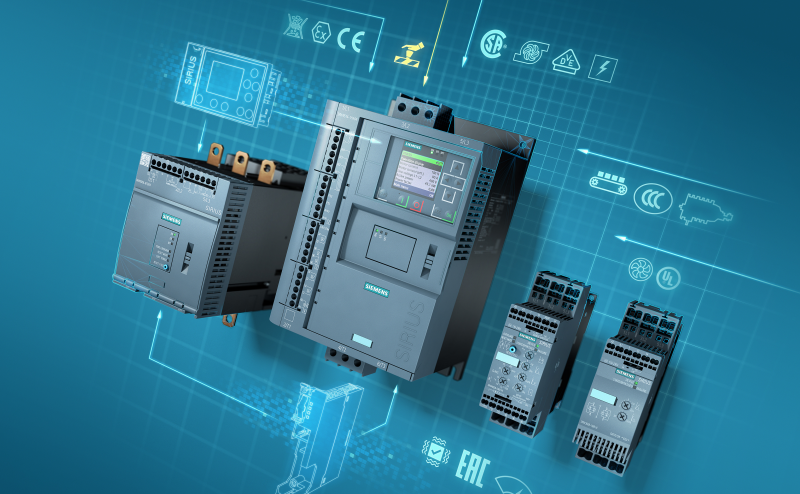
To do this, soft starters often use solid-state devices, such as thyristors, to control the flow of current. These devices manage one to three phases of the power supply, with three-phase control typically delivering better performance.
In their normal OFF state, the thyristors limit current flow, while in the ON state, they allow current to pass. During the motor's ramp-up phase, the thyristors adjust the current, and once the motor reaches its full speed, bypass contactors engage to enhance efficiency.
From an efficiency point of view, soft starters automatically reduce the load when the motor reaches full speed — avoiding unnecessary consumption and premature machinery failure.
VFDs
Since the 1980s, the advance of power electronics has reduced the size and cost of the Variable Frequency Drives (VFD). With recent developments in semiconductor switching devices, drive topologies and control hardware and software, VFDs are also now more desirable than ever before.
VFDs control the speed of AC induction motors by varying the frequency of the input supply. Like soft starters, VFDs eliminate inrush currents, decreasing the required torque load by gradually ramping the motor up to speed.
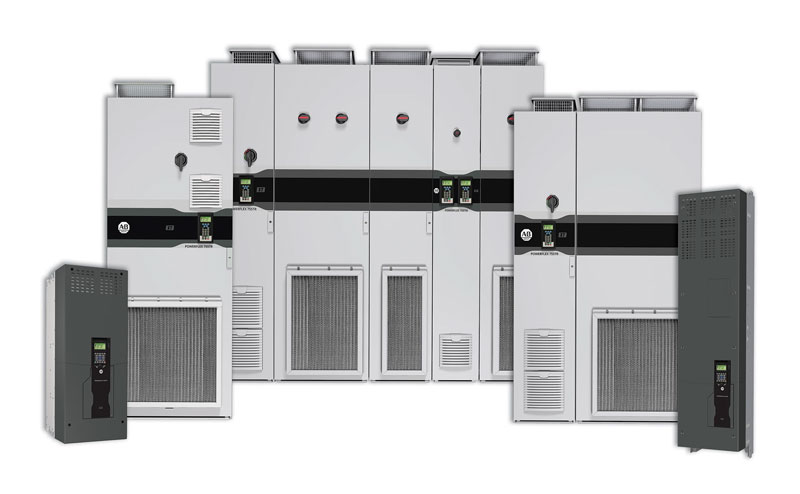
However, rather than providing gentle acceleration to full speed at start-up, VFDs regulate motor speed by modifying the frequency of the sinewave of the supply voltage. Consequently, if motors require speed control during operation, VFDs are recommended over soft starters.
Although it’s believed that around 80 per cent of electric motors in the world are still not controlled by a VFD, they offer substantial benefits, particularly in improving energy efficiency by up to 80 per cent.
With that in mind, a significant advantage is their ability to reduce energy consumption by adjusting motor speeds according to demand, rather than running motors at full speed continuously.
For instance, VFDs in HVAC systems have shown a 25 per cent reduction in energy usage, translating into both financial savings and a reduced environmental footprintâ.
Brushed and brushless
We also have DC motors, which run on direct current (DC) electricity. Unlike AC motors, which are powered by alternating current, DC motors are powered by a constant flow of electricity in one direction.
An option is brushless DC motors (BLDC), which use electronic controllers to manage the direction of current in the stator's winding, a process known as electronic commutation. This allows the controller to switch the current quickly when needed.
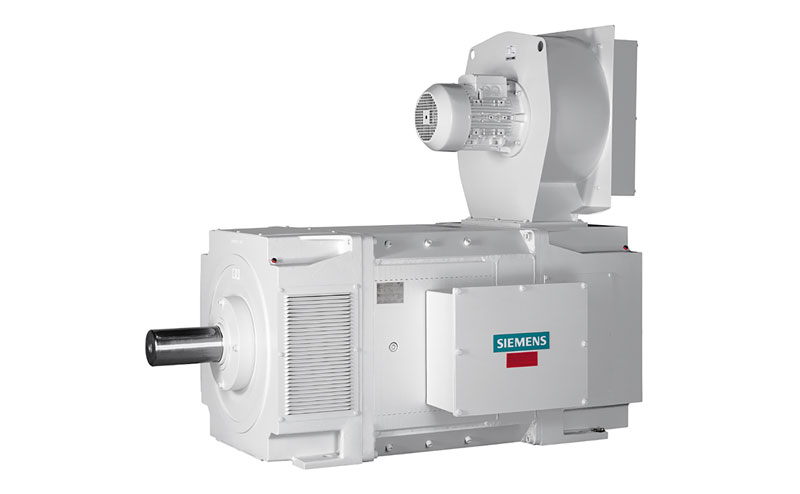
Alternatively, manufacturers can also use a brushed DC (BDC) controller. These regulate the motor’s speed and torque by regulating the speed and current injected into it, allowing the motor to start, stop and change direction.
Determining the right option for you comes down to one important factor — your application. After all, the costs and benefits of each technology can vary widely depending on the industry and application requirements.
This comes as, globally, approximately two billion electric motors are produced annually. Therefore, it’s clear to see that these motors are a critical component in many industrial facilities, yet they are among the largest energy consumers.
By carefully considering your application and selecting the appropriate solution — whether it’s a soft starter, a VFD or a Stepper Drive — manufacturers can achieve more effective motor control.
Partnering with a reputable automation parts supplier, such as Foxmere, can provide access to a wide range of replacement parts and technologies, helping to optimise energy consumption and enhance operational efficiency.
For advice on motor control, or if you’re looking for spare automation parts, contact one of our expert team today.