Why machines break: Causes of production line downtime
Machines break. It's inevitable. It's a fact of life.
When those machines are part of an automated production line, it can cost huge amounts of money. Forbes reports that unplanned downtime is one of the most expensive problems for industrial or manufacturing plants.
Over the past three years, 82% of businesses have experienced at least two production line problems and, on average, unscheduled downtime is costing manufacturers a staggering $50 billion per year.
So, what are the reasons for production line failure, and how can we prevent it from happening?
Causes of production line failure
2019 research from iBase-t shows that the top causes of unplanned production line downtime are equipment failure, human error, and tooling changeovers. However, it's worth noting that human error feeds into other aspects of equipment failure. Let's deal with that one first.
1. Human error
Although machines can go wrong on their own, it's not unusual for issues to be caused by human operators. From incorrect setup or calibration of equipment, and misalignment of parts and materials, to wiring issues, poor programming, or simply not using a machine correctly, human error is a common cause of unplanned downtime.
2. Poor maintenance
Mechanical failures are probably the single most common cause of unexpected downtime. Often, machines break because of poor or non-existent planned maintenance routines.
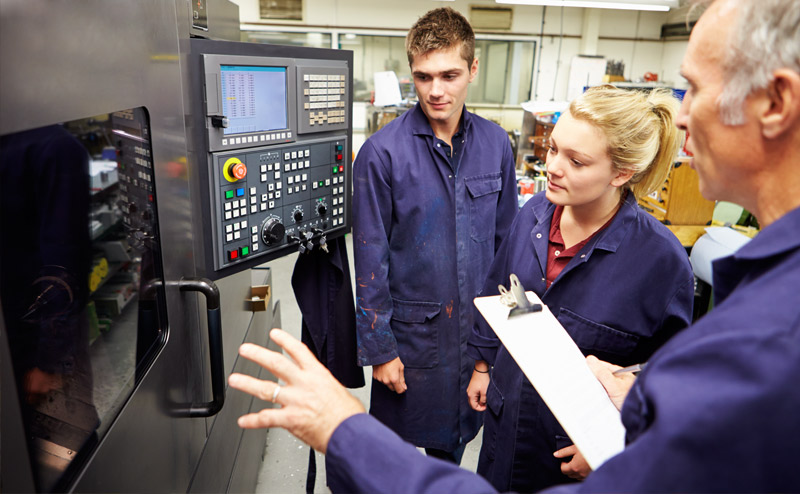
Lack of proper maintenance can cause components to overheat or wear out prematurely. A good example would be using the wrong lubricant (or not enough) to keep the machine functioning correctly.
What's more, minor problems are exacerbated if not spotted early. Very quickly, a slight problem with one part of the production line could easily affect things further down the line on a more significant level.
3. Environmental factors
Components can be negatively impacted by extreme temperature and humidity, dust and debris build-up, or harsh chemicals.
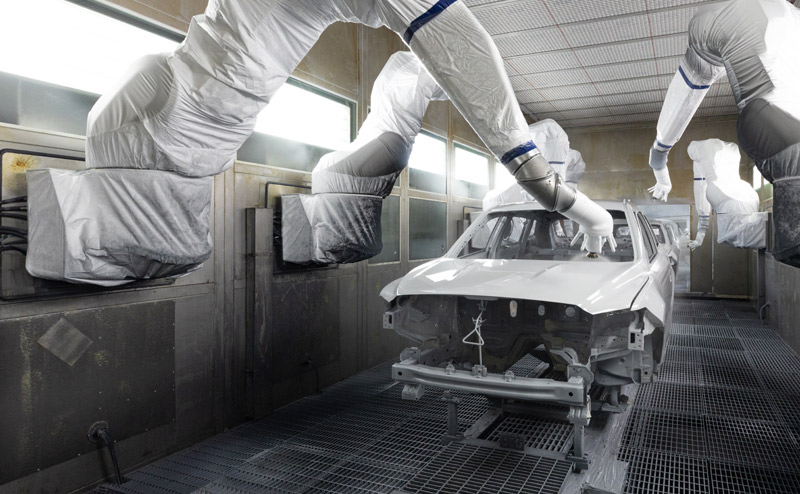
For example, in tropical environments, where there is more humidity, or in an automotive paint shop, where there are particulates in the air, machine hardware may experience a shorter shelf-life than quoted by the OEM.
For these environments, it's not uncommon to see systems integrators and machine builders opting to install conformally-coated hardware. Conformal coatings protect against environmental factors such as moisture, dust, salt, chemicals, temperature changes and mechanical abrasion. Manufacturers like Siemens and Allen-Bradley sell many of their parts with a conformal coating option.
4. Blockages and jams
The proper flow of materials along the line can be disrupted by blockages or improper synchronisation. Predominantly, blockages and jams are caused by misconfigured hardware or materials being loaded incorrectly. If you've ever owned a printer, you'll know how frustrating a jam can be!
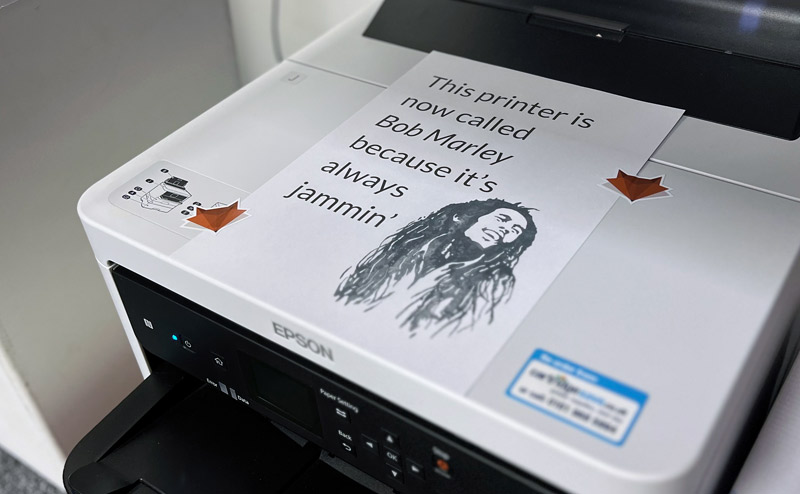
An example of automation failure: The Mars Climate Orbiter
An interesting example of an automation failure with catastrophic consequences is NASA's Mars Climate Orbiter. While not a traditional production line, the unsuccessful mission shows the importance of attention to detail when automation is involved.
One mistake ruined everything.
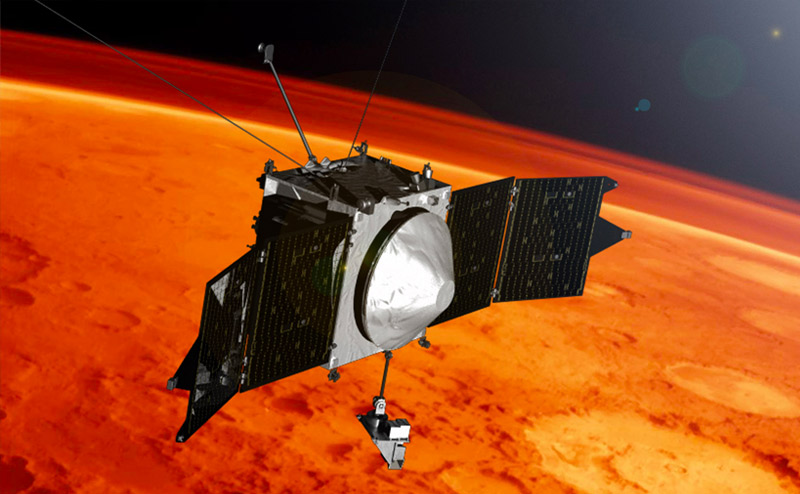
The Mars Climate Orbiter spacecraft launched in December 1998. The mission aimed to study Mars from orbit, but the spacecraft ended up burning in the Martian atmosphere. This was due to a navigation error that caused the spacecraft to approach Mars at too low of an altitude.
The reason? A failure to convert units of measurement between imperial (pound-seconds) and metric (Newton-seconds). Essentially, it's a classic case of human error.
Possible solutions
Most businesses rely on reactive or breakdown maintenance measures to combat unscheduled downtime. That means waiting for machines to fail before performing any repairs.
Reactive maintenance may seem quick and cost-effective, but statistically, it's not.
Unscheduled maintenance will increase downtime and carry higher installation and procurement costs.
The key to reducing machine failure is adopting a robust preventative maintenance schedule, proper training, efficient quality control and thorough troubleshooting processes.
Find out more about preventative maintenance here. Or get in touch if you need help sourcing parts.