The three Ps of mass production
240 years ago, American inventor Oliver Evans laid the foundation for mass production with the first fully automated flour mill, powered by water and mostly made of wood.
Before Evans invented his automated mill, the product of various milling processes required significant manual input. For example, raw grain had to be carried to the top of the mill for grinding, and freshly ground flour then had to be manually raked to allow it to dry.
Evans developed various machinery that worked in concert, such as conveyors, bucket elevators and automated raking machines, creating an interconnected system which only required humans to manage the machinery and oversee the process.
Evans' system met three core requirements:
- Purity: the flour was free from moisture and contaminants.
- Precision: flour came out evenly ground, at a consistent quality.
- Productivity: producing flour cost less than the traditional method.
Arguably, the value of any modern automated manufacturing system comes from how well it performs against the same three requirements.
Purity
Today, quality control involves much more than checking flour for grit or small stones. Modern manufacturing products are rigorously inspected to ensure they meet high standards of purity and quality, such as checking for material integrity, dimensional accuracy and functional performance.
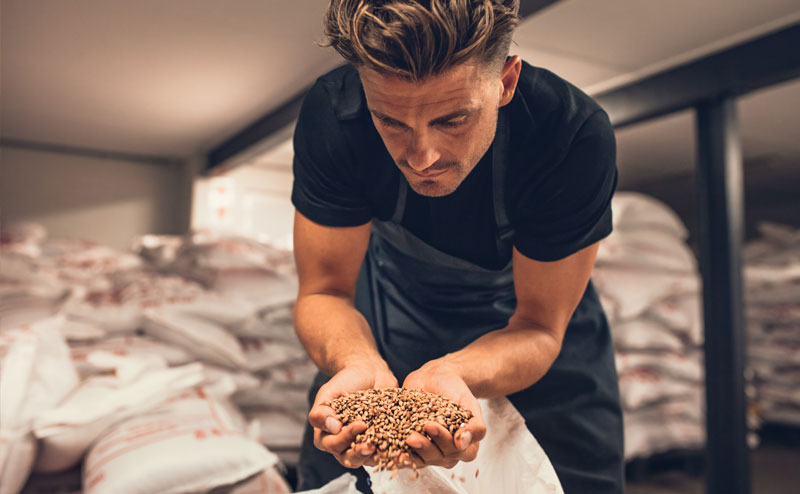
Freedom from contaminants or defects is especially significant in regulated industries such as healthcare, automotive or aerospace, where any output that fails to meet certain standards leads to scrap and wastage, increasing costs. If not identified before leaving the factory, issues can lead to expensive product recalls and disappointed customers.
Precision
One of automation's many benefits is its ability to eliminate the potential for human error. Evans' automatic raking and drying machine ensured the mill's flour maintained a consistent moisture content.
Similarly, modern automated manufacturing must produce parts with uniform characteristics to ensure that customers can rely on consignments to meet their requirements. An inconsistent batch or frequent rework indicates a potential issue within the manufacturing system.
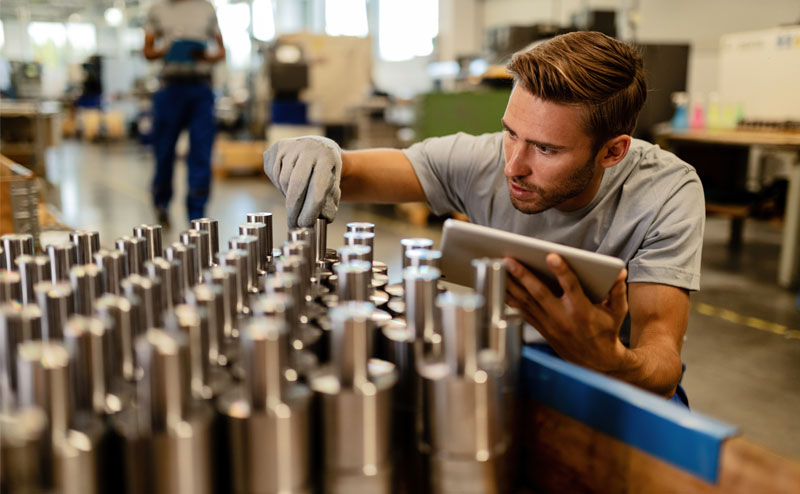
The system itself also calls for precision, and components such as motors or encoders, actuators and control units must meet precise specifications to ensure they fit and function correctly within automated systems. Any replacement parts must be guaranteed to be exact matches.
Productivity
Today, by integrating advanced machinery and robotics, production processes are streamlined, labour costs are reduced and output is increased.
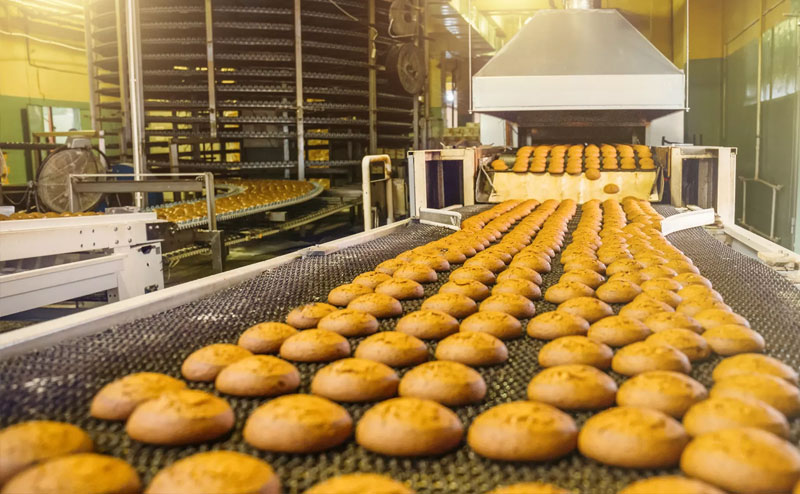
Such a three-pronged approach not only maximises efficiency and productivity but also frees up human capacity for more critical and complex tasks. What's more, this integration is part of quality assurance, ensuring that all components work together effectively to maintain the quality and reliability of the manufacturing process.
Evans' system received the USA's third ever patent, signed by George Washington himself. Washington was so impressed that he implemented the system at his own mill, which still operates 240 years later.
Evans created a system that was worth more than the sum of its parts, and with automation, so can you. For support developing your own system or for spare automation parts to maintain your existing system, speak with one of our experts today.